PRODUCT LABELLING
Before delivery, the supplier marks its products with the information required by Coca-Cola HBC Austria using globally unique application identifiers (AI) from GS1 in the form of the GS1 transport label.
This includes the information: GTIN, quantity, pallet height, BBD, batch and SSCC. Upon delivery, the pallets can be immediately collected by Coca-Cola HBC Austria with all additional information and used for downstream processes without any additional effort.
WAREHOUSING
Several block storage areas as well as the area of the mobile racks from the Still company are captured by our system. Each space is assigned to a zone and has different space characteristics and attributes such as height, width, maximum weight per space, compartment and field, bio-zone, pallet type (industrial pallet, e-pallet, mesh box, …) including prioritisation of the pallet type. The allocation of the products to the different storage areas and zones, which enables the optimal utilisation of the overall system, is stored in the master data and can be flexibly adjusted in the control station based on the production requirements.
STORAGE AND REMOVAL STRATEGIES
In order to optimally organise the more than 500 pallet movements per day, various optimisation strategies are used at the same time, which are controlled and monitored by our system. Batch FIFO, for example, ensures that the oldest products are taken out of storage first. The combination of “store near next load” strategies with “double play” reduces empty runs to a minimum, maximising the productivity of the folklift and their operators.
In the background, algorithms ensure that various criteria are met in order to determine a pitch that corresponds to the relevant attributes. For example, field load monitoring ensures that racks and shelves are never overloaded. Organic products can only be stored in an organic zone, the height control distributes pallets according to the storage space height and thus ensures the highest possible storage density.
Batches containing articles that require testing are automatically blocked on delivery and placed in quarantine until they are released for production following internal checks. Products that are put back into stock from the production line are returned to the warehouse in a returns process. The number of products still on the pallet and the current pallet height are determined at the weighing station. An updated item label is automatically printed and the storage process is automatically started.
FORKLIFTS UPGRADE
Each forklift was easily upgraded with a forklift terminal and thus integrated into our system. At the terminal, the operator can enter pallets, adjust and edit detailed information such as pallet type, height, weight, number of pieces, and much more. It determines the route to the optimal parking space that meets the criteria entered. A direct interface from the forklift to the mobile rack enables direct control and thus efficient management of the entire warehouse.
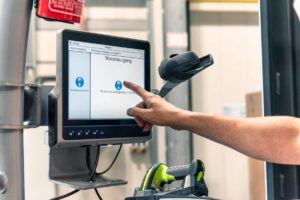
CONTROL CENTRE
All activities can be conveniently analysed and controlled on the browser via a modern dashboard.
The information obtained, such as the real-time stock level or even a complete master data overview, enables efficient planning for procurement and production.
Thanks to batch management and booking logs, you always have an up-to-date view of all processes in the warehouse at the control station, and faults and shortages are detected immediately.