Solution
A solution based on RFID technology was introduced to make the return process and the storage and retrieval of products much more efficient. Each product is clearly marked with an RFID tag, and all workstations are equipped with RFID reading stations. This makes it possible to capture up to 150 products simultaneously at the individual stations in a matter of seconds. Via an interface to the warehouse system, the contents of the shipping carton or small part HU are exchanged with the fully automated warehouse or the customer’s ERP system. Incorrectly associated products or products that do not meet certain criteria (such as best-before date) are immediately displayed to the user and lead to a minimisation of the error rate of up to 100%.

Product labelling
Through tests in our RFID measurement laboratory, we have evaluated the ideal label for the different product groups. All products are subject to the UDI labelling obligation for the unique identification of medical devices – this also had to be taken into account in the coding scheme of the transponders. All newly manufactured products from implantcast are provided with this RFID label during production. The transponders are programmed automatically on the applicator or manually at a TeachIn workstation. This contains a wide range of information such as GTIN, serial number, best before date, etc. From this station, the labelled products are transferred to the fully automated warehouse of KNAPP AG and stored there until ordered.
Incoming goods
The returns with the different, unneeded products from the hospitals accepted and sorted into a marked small part HU. This small part HU is pushed from the workstation directly onto the conveyor system and transported away fully automatically. The uniquely marked products are recorded on our workplace in a matter of seconds and clearly assigned to the small part HU.
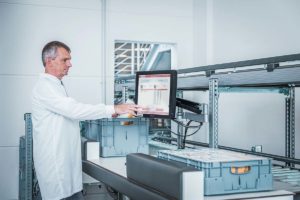
Outgoing goods
As soon as an order is received from a hospital, a picking order is created. The small part HUs containing the required products are automatically brought to the picking workstation by shuttles and conveyor technology. There, the required product is removed and placed in the target container belonging to the order. This target container is forwarded to our RFID workplace for packing. There, a target/actual comparison of the products belonging to the order takes place. Correct products are marked in green, wrong products or products that do not fulfil certain criteria, such as best-before date, are marked in red on the screen. This enables an immediate visual check, it can be determined in seconds whether the order is complete and correct.

Buffer station
Since not all orders can be picked by type and in series due to the high product throughput, semi-finished shipping cartons are buffered temporarily. Our software manages the buffer storage bins with the shipping cartons booked on them and the associated shipping orders. If additional target containers for a temporarily buffered order arrive, the location of the associated shipping box is visually highlighted on the screen. This can be removed and further processed at the neighbouring RFID workstation.
Rfid Gate
The completely filled shipping box is taken to the goods issue warehouse and collected there by the shipping service provider. The shipping carton passes through our RFID gate when it enters this warehouse. When driving through, the tags and their direction of movement are detected. If they come into the warehouse, a shipping label is automatically printed for the box; if a product moves in the other direction, back into the warehouse, an automatic chargeback takes place.